Disc parts are one of the typical parts commonly seen in machining. The main types of disc parts include: various bearings supporting the transmission shaft, flanges, bearing discs, pressure plates, end covers, collar transparent covers, etc. Each has its own unique shape and function. The quality of these parts directly affects the operating efficiency and safety of the equipment. Therefore, there are strict requirements for the manufacturing process and quality control of disc parts.
Contents
Part 1: Analysis of processing technology of disc parts
Part 2: Processing accuracy control of disk parts
Part 3: Material selection for disc parts
Part 4: Heat treatment of disc parts
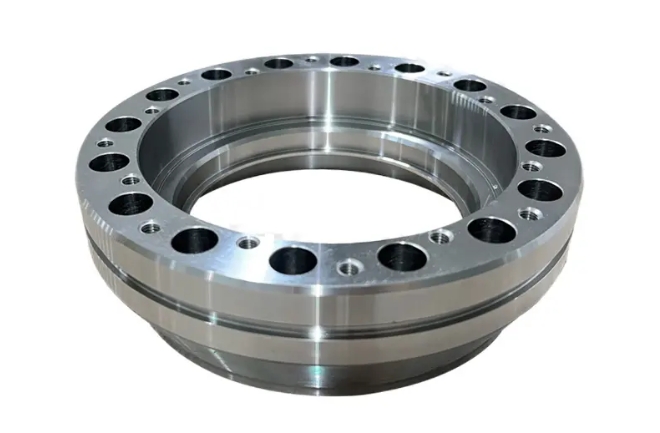
Part 1: Analysis of processing technology of disc parts
The main processes of disc parts processing are mostly roughing and finishing of the inner hole and outer surface, especially the roughing and finishing of the hole are the most important. Commonly used processing methods include drilling, reaming, comparing holes, grinding holes, drawing holes, grinding holes, etc. Among them, drilling, reaming, and canopy holes are generally used as rough machining and semi-finishing of holes. Keyholes, grinding holes, etc. Holes, drawn holes and ground holes are the finishing of holes. When determining the hole processing plan, the following principles are generally followed.
1) For holes with smaller diameters, the solution of drilling, expanding and drilling is mostly adopted.
2) For holes with larger diameters, most of them adopt the solution of drilling and further finishing.
3) For quenched steel or sleeve parts with higher precision requirements, the hole grinding solution must be adopted.
Disc parts are relatively complex structural parts composed of multiple end faces, deep holes, curved surfaces and outer contours. Therefore, they mainly play a supporting and connecting role in mechanical equipment. According to the specific part characteristics and requirements, it is necessary to select appropriate processing methods and process parameters, and at the same time carry out strict quality control during the processing. For example, for thin-walled disk parts, due to poor stiffness, improper selection of clamping position, clamping force, and clamping scheme during processing can easily cause clamping deformation, seriously affecting the processing accuracy of the parts. Therefore, optimizing the clamping layout and clamping force parameters is a key step to reduce clamping deformation.
Part 2: Processing accuracy control of disk parts
Precision control is also an important part of the machining of disk parts. This includes control of dimensional accuracy, shape accuracy and positional accuracy. For example, for some disc parts with high precision requirements, such as the dimensional accuracy of the inner hole is IT6, the cylindricity requirement of some holes and outer circles is ≤0.02 mm, the flatness requirement of the large end face and small end face is ≤0.02 mm, and the requirements with the hole The verticality requirement is ≤0.02 mm. This requires the use of high-precision equipment and tools during the machining process, while also ensuring high precision in depth.
Part 3: Material selection for disc parts
Disc parts are often made of steel, cast iron, bronze or brass. Disks with small holes generally choose hot-rolled or cold-drawn bars. Depending on the material, solid castings can be selected; when the hole diameter is larger, pre-holes can be made. If the production batch is large, advanced blank manufacturing processes such as cold extrusion can be selected to improve productivity and save materials.
Part 4: Heat treatment of disc parts
1) The heat treatment processes for disc parts include normalizing, annealing, quenching and tempering, carburizing and quenching, high-frequency induction quenching, nitriding, aging, oil boiling and characterization, etc.
2) Commonly used heat treatment equipment include box furnaces, multi-purpose furnaces, high-frequency induction quenching machine tools, carburizing furnaces, nitriding furnaces, tempering furn
GPM’s Machining Capabilities:
GPM has 20 years experience in CNC machining of different kinds of precision parts. We have worked with customers in many industries, including semiconductor, medical equipment, etc., and are committed to providing customers with high-quality, precise machining services. We adopt a strict quality management system to ensure that every part meets customer expectations and standards.
Copyright notice:
GPM Intelligent Technology(Guangdong) Co., Ltd. advocates respect and protection of intellectual property rights and indicates the source of articles with clear sources. If you find that there are copyright or other problems in the content of this website, please contact us to deal with it. Contact information: marketing01@gpmcn.com
Post time: Jan-16-2024