加工偏差とは、加工後の部品の実際の幾何学的パラメータ (サイズ、形状、位置) と理想的な幾何学的パラメータとの差を指します。機械部品の加工誤差には、原理誤差、クランプ誤差、工作機械や治具の製造や磨耗に起因する誤差など、工作機械、治具、切削工具、ワークから構成されるプロセスシステムにおける多くの誤差要因を含め、さまざまな原因があります。や切削工具など。
コンテンツ
第 1 部: 工作機械の製造上のばらつき
パート 2: 工具の幾何学的偏差
パート 3: 治具の幾何学的偏差
パート 4: プロセス システムの熱変形によって生じる偏差
パート 4: 内部ストレス

第 1 部: 工作機械の製造上のばらつき
工作機械の製造誤差は、加工されるワークの精度に影響を与えます。工作機械のさまざまな誤差のうち、ワークの加工精度に大きな影響を及ぼす主なものは、主軸の回転誤差とガイドレールの誤差です。主軸の回転誤差は主軸ベアリングの摩耗、主軸の曲がり、主軸の軸方向の動きなどによって発生しますが、ガイドレールの誤差はガイドレール表面の摩耗、ガイドレールのクリアランスの大きすぎ、小さすぎなどによって発生します。
工作機械の製造誤差が加工対象のワークの精度に与える影響を回避するために、次のような対策を講じることができます。
a.高精度で安定性の高い工作機械を選択してください。
b.工作機械を良好な潤滑状態に保ちます。
c.工作機械を清潔に保ち、ガイド レールのペアに塵やその他の不純物が入らないようにしてください。
d.適切な治具とツールを使用してください。
パート 2: 工具の幾何学的偏差
工具の幾何学的誤差とは、工具の形状、サイズ、その他の幾何学的パラメータと設計要件との差異を指し、加工されるワークの精度に影響を与えます。工具の幾何学的誤差には主に、工具形状誤差、工具サイズ誤差、工具表面粗さ誤差などが含まれます。
加工中のワークの精度に対する工具の幾何学的誤差の影響を回避するために、次の措置を講じることができます。
a.高精度で安定性の高いツールを選択してください。
b.切削工具は良好な潤滑状態に保ってください。
c.適切な治具と工作機械を使用してください。
パート 3: 治具の幾何学的偏差
治具の幾何学的誤差は、加工されるワークの精度に影響を与えます。治具の幾何学的誤差には主に、位置決め誤差、クランプ誤差、工具設定誤差、工作機械への治具の取り付け誤差などが含まれます。
加工中のワークの精度に対する治具の幾何学的誤差の影響を回避するために、次の措置を講じることができます。
a.高精度の治具を使用してください。
b.治具の位置決めとクランプの精度を厳密に管理します。
c.製造精度が保証する必要があるプロセスの寸法精度と一致するように、治具内の位置決めコンポーネントを正しく選択します。
パート 4: プロセス システムの熱変形によって生じる偏差
加工プロセス中、加工システムは切削熱、摩擦熱、太陽光などにより複雑な熱変形を受け、工具に対するワークの位置や運動関係が変化し、加工誤差が発生します。熱変形誤差は、精密機械加工、大型部品の加工、自動化処理に決定的な影響を与えることがよくあります。
このエラーを回避するには、次の措置を講じることができます。
a.工作機械の構造を最適化し、熱変形を低減します。
b.高品質の冷却剤を使用してください。
c.高品質の潤滑油を使用してください。
d.高品質の素材を使用します。
パート 5: 内部ストレス
内部応力とは、外部荷重を取り除いた後に物体の内部に残る応力を指します。これは、材料内の巨視的または微視的構造の不均一な体積変化によって引き起こされます。ワークに内部応力が発生すると、ワークの金属は高エネルギーの不安定な状態になります。変形を伴い本能的に低エネルギーの安定状態に変化してしまい、ワーク本来の加工精度が失われてしまいます。
機械加工された材料の内部応力は、応力除去焼きなまし、焼き戻し、または自然時効処理、振動および応力除去によって除去できます。中でも歪み取り焼鈍は、溶接残留応力、鋳造残留応力、機械加工残留応力を除去するために最も一般的に使用され、有効な方法の一つです。
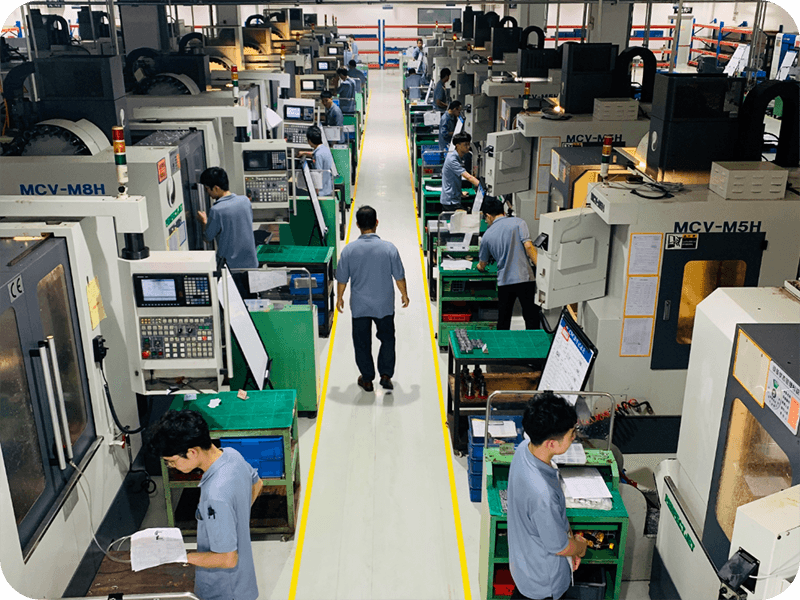
GPMには、豊富な機械加工経験と技術知識を備えた専門の研究開発チームと技術者がおり、お客様のニーズに応じてカスタマイズされたソリューションと最適化された設計を提供し、加工結果がお客様の要件を確実に満たすことができます。同時に、GPM は品質管理を非常に重視しており、完全な品質管理システムと厳格なテスト手順を備えています。最先端の測定器や設備を駆使し、各加工部品が要求事項を満たし、高い精度と品質を実現します。
投稿時間: 2023 年 10 月 5 日