ප්ලාස්ටික් අංශු ප්ලාස්ටික් නිෂ්පාදන බවට පරිවර්තනය කිරීමේ වාත්තු ක්රියාවලියේදී, ප්ලාස්ටික් බොහෝ විට අධික උෂ්ණත්වයට හා අධික පීඩනයකට ලක් වන අතර ඉහළ කැපුම් අනුපාතයකින් ප්රවාහ අච්චු ගැසීම සිදු කරයි.විවිධ අච්චු තත්ත්වයන් සහ ක්රියාවලීන් නිෂ්පාදනයේ ගුණාත්මකභාවය කෙරෙහි විවිධ බලපෑම් ඇති කරයි.ඉන්ජෙක්ෂන් මෝල්ඩින් ප්ලාස්ටික් ඇත එය පැති හතරකින් සමන්විත වේ: අමුද්රව්ය, එන්නත් අච්චු යන්ත්රය, අච්චුව සහ එන්නත් අච්චු ගැසීමේ ක්රියාවලිය.
නිෂ්පාදනවල ගුණාත්මකභාවය අභ්යන්තර ද්රව්යයේ ගුණාත්මකභාවය සහ පෙනුමේ ගුණාත්මකභාවය ඇතුළත් වේ.අභ්යන්තර ද්රව්යයේ ගුණාත්මකභාවය ප්රධාන වශයෙන් යාන්ත්රික ශක්තිය වන අතර අභ්යන්තර ආතතියේ ප්රමාණය නිෂ්පාදනයේ යාන්ත්රික ශක්තියට සෘජුවම බලපායි.අභ්යන්තර ආතතිය උත්පාදනය කිරීම සඳහා ප්රධාන හේතු තීරණය වන්නේ නිෂ්පාදනයේ ස්ඵටිකතාවය සහ ප්ලාස්ටික් අච්චුවෙහි අණු දිශානතියයි.වල.නිෂ්පාදනයේ පෙනුමේ ගුණාත්මක භාවය නිෂ්පාදනයේ මතුපිට ගුණාත්මක භාවය වේ, නමුත් විශාල අභ්යන්තර ආතතිය හේතුවෙන් නිෂ්පාදනයේ විකෘති වීම සහ විරූපණය ද පෙනුමේ ගුණාත්මක භාවයට බලපානු ඇත.නිෂ්පාදනවල පෙනුමේ ගුණාත්මක භාවයට ඇතුළත් වන්නේ: ප්රමාණවත් නොවන නිෂ්පාදන, නිෂ්පාදන ඩෙන්ට්, වෙල්ඩ් ලකුණු, ෆ්ලෑෂ්, බුබුලු, රිදී වයර්, කළු ලප, විරූපණය, ඉරිතැලීම්, දිරාපත්වීම, පීල් කිරීම සහ දුර්වර්ණ වීම යනාදිය, අච්චු උෂ්ණත්වය, පීඩනය, ප්රවාහය, කාලය හා සම්බන්ධ සහ තනතුර.සම්බන්ධයි.
අන්තර්ගතය
පළමු කොටස: වාත්තු උෂ්ණත්වය
දෙවන කොටස: වාත්තු ක්රියාවලිය පීඩනය
තුන්වන කොටස: ඉන්ජෙක්ෂන් මෝල්ඩින් යන්ත්රයේ වේගය
හතරවන කොටස: වේලාව සැකසීම
පස්වන කොටස: ස්ථාන පාලනය
පළමු කොටස: වාත්තු උෂ්ණත්වය
බැරල් උෂ්ණත්වය:එය ප්ලාස්ටික් වල දියවන උෂ්ණත්වයයි.බැරලයක උෂ්ණත්වය ඉතා ඉහළ මට්ටමක පවතී නම්, දියවීමෙන් පසු ප්ලාස්ටික් දුස්ස්රාවීතාවය අඩු වේ.එකම එන්නත් පීඩනය සහ ප්රවාහ අනුපාතය යටතේ, එන්නත් කිරීමේ වේගය වේගවත් වන අතර, අච්චු නිෂ්පාදන ෆ්ලෑෂ්, රිදී, දුර්වර්ණ වීම සහ අස්ථාවරත්වයට ගොදුරු වේ.
බැරලයේ උෂ්ණත්වය ඉතා අඩුය, ප්ලාස්ටික් දුර්වල ලෙස ප්ලාස්ටික් වී ඇත, දුස්ස්රාවීතාවය ඉහළ ය, එන්නත් කිරීමේ වේගය එකම එන්නත් පීඩනය සහ ප්රවාහ අනුපාතය යටතේ මන්දගාමී වේ, අච්චු නිෂ්පාදන පහසුවෙන් ප්රමාණවත් නොවේ, වෑල්ඩින් ලකුණු පැහැදිලිය, මානයන් වේ අස්ථායී වන අතර නිෂ්පාදනවල සීතල කුට්ටි ඇත.
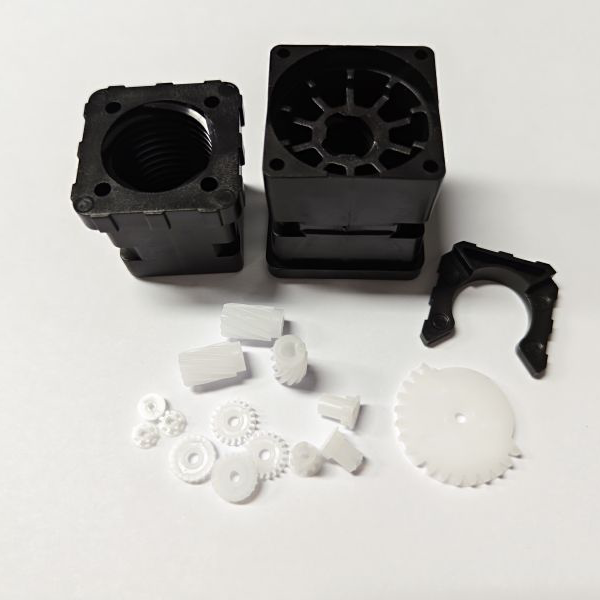
තුණ්ඩ උෂ්ණත්වය:තුණ්ඩයේ උෂ්ණත්වය ඉහළ මට්ටමක පවතී නම්, තුණ්ඩය පහසුවෙන් ගලා යන අතර නිෂ්පාදනයේ සීතල සූතිකා ඇති කරයි.අඩු තුණ්ඩ උෂ්ණත්වය පුස් වත් කිරීමේ පද්ධතිය අවහිර වීමට හේතු වේ.ප්ලාස්ටික් එන්නත් කිරීම සඳහා එන්නත් පීඩනය වැඩි කළ යුතුය, නමුත් වහාම වාත්තු කරන ලද නිෂ්පාදනයේ සීතල ද්රව්ය පවතිනු ඇත.
අච්චු උෂ්ණත්වය:අච්චු උෂ්ණත්වය ඉහළ නම්, එන්නත් පීඩනය සහ ප්රවාහ අනුපාතය අඩු කළ හැක.කෙසේ වෙතත්, එකම පීඩනය සහ ප්රවාහ අනුපාතය, නිෂ්පාදනය පහසුවෙන් දැල්වෙන, විකෘති සහ විකෘති වන අතර, එය අච්චුවෙන් නිෂ්පාදිතය ඉවත් කිරීමට අපහසු වනු ඇත.අච්චු උෂ්ණත්වය අඩු වන අතර, එම එන්නත් පීඩනය සහ ප්රවාහ අනුපාතය යටතේ, නිෂ්පාදනය ප්රමාණවත් ලෙස පිහිටුවා ඇත, බුබුලු සහ වෑල්ඩින් සලකුණු ආදිය.
ප්ලාස්ටික් වියළීමේ උෂ්ණත්වය:විවිධ ප්ලාස්ටික් විවිධ වියළන උෂ්ණත්වයන් ඇත.ABS ප්ලාස්ටික් සාමාන්යයෙන් වියළන උෂ්ණත්වය 80 සිට 90 ° C දක්වා සකසයි, එසේ නොමැතිනම් තෙතමනය හා අවශේෂ ද්රාවක වියළීමට හා වාෂ්ප කිරීමට අපහසු වන අතර නිෂ්පාදනවලට පහසුවෙන් රිදී වයර් සහ බුබුලු ඇති අතර නිෂ්පාදනවල ශක්තියද අඩු වේ.
දෙවන කොටස: වාත්තු ක්රියාවලිය පීඩනය
පූර්ව වාත්තු පිටුපස පීඩනය:ඉහළ පිටුපස පීඩනය සහ ඉහළ ගබඩා ඝනත්වය යනු එකම ගබඩා පරිමාවක් තුළ වැඩි ද්රව්ය ගබඩා කළ හැකි බවයි.අඩු පිටුපස පීඩනය යනු අඩු ගබඩා ඝනත්වය සහ අඩු ගබඩා ද්රව්යය.ගබඩා ස්ථානය සැකසීමෙන් පසුව, පසුපස පීඩනයට විශාල ගැලපීමක් සිදු කිරීමෙන් පසුව, ගබඩා ස්ථානය නැවත සැකසීමට ඔබ අවධානය යොමු කළ යුතුය, එසේ නොමැතිනම් එය පහසුවෙන් ෆ්ලෑෂ් හෝ ප්රමාණවත් නිෂ්පාදනයක් ඇති කරයි.
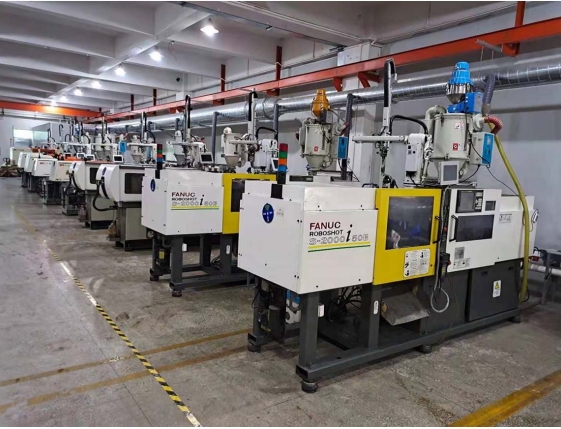
එන්නත් පීඩනය:විවිධ ප්ලාස්ටික් වර්ගවල විවිධ දියවන දුස්ස්රාවීතාවයන් ඇත.ප්ලාස්ටික්කරණ උෂ්ණත්වයේ වෙනස්වීම් සමඟ අස්ඵටික ප්ලාස්ටික්වල දුස්ස්රාවීතාවය විශාල වශයෙන් වෙනස් වේ.ප්ලාස්ටික් වල වෙල්ඩින් දුස්ස්රාවීතාවය සහ ප්ලාස්ටික් ක්රියාවලිය අනුපාතය අනුව එන්නත් පීඩනය සකස් කර ඇත.එන්නත් පීඩනය ඉතා අඩු ලෙස සකසා ඇත්නම්, නිෂ්පාදිතය ප්රමාණවත් ලෙස එන්නත් කරනු ලැබේ, එහි ප්රතිඵලයක් ලෙස දත්, වෑල්ඩින් ලකුණු සහ අස්ථායී මානයන් ඇති වේ.එන්නත් පීඩනය ඉතා ඉහළ නම්, නිෂ්පාදනයට ෆ්ලෑෂ්, අවපැහැ ගැන්වීම සහ අච්චුව පිටකිරීමේ අපහසුතාවයක් ඇත.
තද කිරීමේ පීඩනය:එය අච්චු කුහරයේ ප්රක්ෂේපිත ප්රදේශය සහ එන්නත් පීඩනය මත රඳා පවතී.කලම්ප පීඩනය ප්රමාණවත් නොවේ නම්, නිෂ්පාදිතය පහසුවෙන් දැල්වෙන අතර බර වැඩිවේ.කලම්ප බලය ඉතා විශාල නම්, අච්චුව විවෘත කිරීමට අපහසු වනු ඇත.සාමාන්යයෙන්, කලම්ප පීඩන සැකසුම 120par/cm2 නොඉක්මවිය යුතුය.
රඳවා තබා ගැනීමේ පීඩනය:එන්නත් කිරීම අවසන් වූ විට, ඉස්කුරුප්පුව රඳවා තබා ගැනීමේ පීඩනය ලෙස හඳුන්වන පීඩනය දිගටම ලබා දෙයි.මෙම අවස්ථාවේදී, අච්චු කුහරය තුළ නිෂ්පාදිතය තවමත් ශීත කර නැත.නිෂ්පාදනය පිරී ඇති බව සහතික කිරීම සඳහා පීඩනය පවත්වා ගැනීම අච්චු කුහරය පිරවීම දිගටම කරගෙන යා හැක.රඳවා තබා ගැනීමේ පීඩනය සහ පීඩන සැකසුම ඉතා ඉහළ නම්, එය ආධාරක අච්චුව සහ ඇදගෙන යාමේ හරයට විශාල ප්රතිරෝධයක් ගෙන එනු ඇත.නිෂ්පාදිතය පහසුවෙන් සුදු හා විකෘති වනු ඇත.මීට අමතරව, අච්චු ධාවන ගේට්ටුව පරිපූරක ප්ලාස්ටික් මගින් පහසුවෙන් පුළුල් කර තද කර ඇති අතර, ගේට්ටුව ධාවකය තුළ කැඩී යයි.පීඩනය ඉතා අඩු නම්, නිෂ්පාදනයේ දත් සහ අස්ථායී මානයන් ඇත.
ඉෙජක්ටරය සහ නියුට්රෝන පීඩනය සැකසීමේ මූලධර්මය වන්නේ අච්චු කුහරයේ ප්රදේශයේ සමස්ත ප්රමාණය, ඇතුළු කරන ලද හරයේ මූලික ප්රක්ෂේපණ ප්රදේශය සහ අච්චු නිෂ්පාදනයේ ජ්යාමිතික සංකීර්ණත්වය මත පදනම්ව පීඩනය සැකසීමයි.ප්රමාණය.සාමාන්යයෙන්, මෙම නිෂ්පාදනය තල්ලු කිරීමට හැකි වන පරිදි ආධාරක අච්චුවේ සහ නියුට්රෝන සිලින්ඩරයේ පීඩනය සැකසීම අවශ්ය වේ.
තුන්වන කොටස: ඉන්ජෙක්ෂන් මෝල්ඩින් යන්ත්රයේ වේගය
ඉස්කුරුප්පු වේගය: පූර්ව-ප්ලාස්ටික් ප්රවාහ අනුපාතය සකස් කිරීමට අමතරව, එය ප්රධාන වශයෙන් බලපානු ලබන්නේ පූර්ව ප්ලාස්ටික් පසුපස පීඩනයයි.පෙර අච්චු ප්රවාහ අනුපාතය විශාල අගයකට සකසන්නේ නම් සහ පෙර අච්චු පිටුපස පීඩනය ඉහළ නම්, ඉස්කුරුප්පු ඇණ භ්රමණය වන විට, ප්ලාස්ටික් බැරලයේ විශාල කැපුම් බලයක් ඇති අතර ප්ලාස්ටික් අණුක ව්යුහය පහසුවෙන් කපා හැරේ. .නිෂ්පාදනයේ කළු ලප සහ කළු ඉරි ඇති අතර එය නිෂ්පාදනයේ පෙනුමේ ගුණාත්මකභාවය සහ ශක්තියට බලපානු ඇත., සහ බැරල් උණුසුම් උෂ්ණත්වය පාලනය කිරීමට අපහසු වේ.පූර්ව-ප්ලාස්ටික් ප්රවාහ අනුපාතය ඉතා අඩු ලෙස සකසා ඇත්නම්, පූර්ව ප්ලාස්ටික් ගබඩා කිරීමේ කාලය දීර්ඝ කරනු ලැබේ, එය අච්චු චක්රයට බලපානු ඇත.
එන්නත් වේගය:එන්නත් කිරීමේ වේගය සාධාරණ ලෙස සැකසිය යුතුය, එසේ නොමැතිනම් එය නිෂ්පාදනයේ ගුණාත්මක භාවයට බලපානු ඇත.එන්නත් කිරීමේ වේගය ඉතා වේගවත් නම්, නිෂ්පාදනයේ බුබුලු, පිළිස්සුම්, දුර්වර්ණ යනාදිය ඇත. එන්නත් කිරීමේ වේගය ඉතා මන්දගාමී නම්, නිෂ්පාදිතය ප්රමාණවත් නොවීම සහ වෑල්ඩින් සලකුණු ඇත.
ආධාරක අච්චු සහ නියුට්රෝන ප්රවාහ අනුපාතය:ඉතා ඉහළ ලෙස සකසා නොගත යුතුය, එසේ නොමැති නම් පිටකිරීමේ සහ හරය ඇදීමේ චලනයන් ඉතා වේගවත් වනු ඇත, එහි ප්රතිඵලයක් ලෙස අස්ථායී පිටකිරීම් සහ හරය ඇදීම සිදු වන අතර නිෂ්පාදනය පහසුවෙන් සුදු පැහැයට හැරේ.
හතරවන කොටස: වේලාව සැකසීම
වියළීමේ කාලය:ප්ලාස්ටික් අමුද්රව්ය වියළීමේ කාලය මෙයයි.විවිධ ප්ලාස්ටික් වර්ගවල ප්රශස්ත වියළන උෂ්ණත්වය සහ වේලාවන් ඇත.ABS ප්ලාස්ටික් වියළීමේ උෂ්ණත්වය 80 ~ 90 ℃ වන අතර වියළීමේ කාලය පැය 2 කි.ABS ප්ලාස්ටික් සාමාන්යයෙන් පැය 24ක් ඇතුළත ජලය 0.2 සිට 0.4% දක්වා අවශෝෂණය කරන අතර, එන්නත් කළ හැකි ජල ප්රමාණය 0.1 සිට 0.2% දක්වා වේ.
එන්නත් කිරීම සහ පීඩනය රඳවා ගැනීමේ කාලය:පරිගණක එන්නත් කිරීමේ යන්ත්රයේ පාලන ක්රමය අදියරවල පීඩනය, වේගය සහ එන්නත් ප්ලාස්ටික් ප්රමාණය සකස් කිරීම සඳහා බහු-අදියර එන්නත් වලින් සමන්විත වේ.අච්චු කුහරය තුළට එන්නත් කරන ලද ප්ලාස්ටික් වේගය නියත වේගයක් ළඟා වන අතර, අච්චු නිෂ්පාදනවල පෙනුම සහ අභ්යන්තර ද්රව්යයේ ගුණාත්මකභාවය වැඩි දියුණු වේ.
එමනිසා, එන්නත් කිරීමේ ක්රියාවලිය සාමාන්යයෙන් කාල පාලනය වෙනුවට ස්ථාන පාලනය භාවිතා කරයි.රඳවා තබා ගැනීමේ පීඩනය කාලය විසින් පාලනය කරනු ලැබේ.රැඳවුම් කාලය දිගු නම්, නිෂ්පාදන ඝනත්වය වැඩි වේ, බර බර, අභ්යන්තර ආතතිය විශාල වේ, demoulding අපහසු වේ, whiten කිරීමට පහසු, සහ අච්චු චක්රය දීර්ඝ වේ.රඳවා තබා ගැනීමේ කාලය ඉතා කෙටි නම්, නිෂ්පාදිතය දත් හා අස්ථායී මානයන් වලට ගොදුරු වේ.
සිසිලන කාලය:නිෂ්පාදනයේ හැඩය ස්ථාවර බව සහතික කිරීමයි.අච්චු කුහරය තුළට එන්නත් කරන ලද ප්ලාස්ටික් නිෂ්පාදනයට අච්චු කිරීමෙන් පසු ප්රමාණවත් සිසිලනය සහ හැඩගැන්වීමේ කාලය අවශ්ය වේ.එසේ නොමැති නම්, අච්චුව විවෘත කරන විට නිෂ්පාදිතය විකෘති කිරීමට සහ විකෘති කිරීමට පහසු වන අතර, පිටකිරීම විකෘති කිරීමට සහ සුදු වීමට පහසුය.සිසිලන කාලය ඉතා දිගු වන අතර එය අච්චු චක්රය දිගු කරන අතර ආර්ථිකමය නොවේ.
පස්වන කොටස: ස්ථාන පාලනය
අච්චු මාරු කිරීමේ ස්ථානය යනු අච්චුව විවෘත කිරීමේ සිට අච්චු වැසීම සහ අගුලු දැමීම දක්වා වූ සම්පූර්ණ චලනය වන දුරයි, එය අච්චු මාරු කිරීමේ ස්ථානය ලෙස හැඳින්වේ.අච්චුව චලනය කිරීමට හොඳම ස්ථානය වන්නේ නිෂ්පාදිතය සුමටව පිටතට ගැනීමට හැකි වීමයි.අච්චුව විවෘත කිරීමේ දුර ප්රමාණය ඉතා විශාල නම්, අච්චු චක්රය දිගු වේ.
අච්චු ආධාරකයේ පිහිටීම පාලනය වන තාක් කල්, අච්චුවෙන් පිටකිරීමේ ස්ථානය පහසුවෙන් ඉවත් කළ හැකි අතර නිෂ්පාදිතය ඉවත් කළ හැකිය.
ගබඩා ස්ථානය:පළමුව, අච්චු නිෂ්පාදනයට එන්නත් කරන ලද ප්ලාස්ටික් ප්රමාණය සහතික කළ යුතු අතර, දෙවනුව, බැරලයේ ගබඩා කර ඇති ද්රව්ය ප්රමාණය පාලනය කළ යුතුය.ගබඩා ස්ථානය එක් පහරකට වඩා පාලනය කරන්නේ නම්, නිෂ්පාදිතය පහසුවෙන් දැල්වෙයි, එසේ නොමැති නම් නිෂ්පාදිතය ප්රමාණවත් ලෙස සෑදෙන්නේ නැත.
බැරලයේ බොහෝ ද්රව්ය තිබේ නම්, ප්ලාස්ටික් දිගු කාලයක් බැරලයේ රැඳී සිටින අතර, නිෂ්පාදිතය පහසුවෙන් මැකී යන අතර අච්චු නිෂ්පාදනයේ ශක්තියට බලපායි.ඊට පටහැනිව, එය ප්ලාස්ටික් ප්ලාස්ටික්කරණයේ ගුණාත්මක භාවයට බලපාන අතර, පීඩනය පවත්වා ගැනීමේදී කිසිදු ද්රව්යයක් අච්චුව තුලට නැවත පිරවීමක් සිදු නොවේ, එහි ප්රතිඵලයක් ලෙස නිෂ්පාදනයේ සහ දත්වල ප්රමාණවත් අච්චු ගැසීමක් සිදු නොවේ.
නිගමනය
ඉන්ජෙක්ෂන් අච්චු කරන ලද නිෂ්පාදනවල ගුණාත්මක භාවයට නිෂ්පාදන සැලසුම් කිරීම, ප්ලාස්ටික් ද්රව්ය, අච්චු සැලසුම් කිරීම සහ සැකසීමේ ගුණාත්මකභාවය, ඉන්ජෙක්ෂන් මෝල්ඩින් යන්ත්ර තේරීම සහ ක්රියාවලි ගැලපීම යනාදිය ඇතුළත් වේ. එන්නත් ක්රියාවලි ගැලපීම යම් ස්ථානයක සිට ආරම්භ කළ නොහැකි නමුත් එන්නත් කිරීමේ ක්රියාවලියේ මූලධර්මයෙන් ආරම්භ විය යුතුය. .ගැටළු පිළිබඳ සවිස්තරාත්මක හා සවිස්තරාත්මකව සලකා බැලීම, විවිධ පැතිවලින් එකින් එක ගැලපීම් සිදු කළ හැකිය, නැතහොත් ගැටළු කිහිපයක් එකවර සකස් කළ හැකිය.කෙසේ වෙතත්, ගැලපුම් ක්රමය සහ මූලධර්මය එකල නිෂ්පාදිත නිෂ්පාදනවල ගුණාත්මකභාවය සහ ක්රියාවලි තත්ත්වයන් මත රඳා පවතී.
පසු කාලය: නොවැම්බර්-15-2023