Dalam proses pencetakan untuk mengubah partikel plastik menjadi produk plastik, plastik sering kali mengalami suhu tinggi dan tekanan tinggi, serta pencetakan aliran dengan laju geser yang tinggi.Kondisi dan proses pencetakan yang berbeda akan berdampak berbeda terhadap kualitas produk.Cetakan injeksi memiliki plastik Terdiri dari empat aspek: bahan baku, mesin cetak injeksi, cetakan dan proses pencetakan injeksi.
Kualitas produk meliputi kualitas bahan internal dan kualitas penampilan.Kualitas bahan internal terutama adalah kekuatan mekanik, dan ukuran tekanan internal secara langsung mempengaruhi kekuatan mekanik produk.Alasan utama timbulnya tekanan internal ditentukan oleh kristalinitas produk dan orientasi molekul dalam cetakan plastik.dari.Kualitas tampilan produk merupakan kualitas permukaan produk, namun lengkungan dan deformasi produk akibat tekanan internal yang besar juga akan mempengaruhi kualitas tampilan.Kualitas penampilan produk meliputi: produk tidak mencukupi, penyok produk, bekas las, kilatan, gelembung, kabel perak, bintik hitam, deformasi, retak, delaminasi, pengelupasan dan perubahan warna, dll., semuanya terkait dengan suhu cetakan, tekanan, aliran, waktu dan posisi.terkait.
Isi
Bagian Satu: Suhu cetakan
Bagian Kedua: Tekanan proses pencetakan
Bagian ketiga: Kecepatan mesin cetak injeksi
Bagian Keempat: Pengaturan waktu
Bagian Kelima: Pengendalian Posisi
Bagian Satu: Suhu cetakan
Suhu barel:Ini adalah suhu leleh plastik.Jika suhu barel disetel terlalu tinggi, viskositas plastik setelah peleburan akan rendah.Di bawah tekanan injeksi dan laju aliran yang sama, kecepatan injeksi cepat, dan produk cetakan rentan terhadap kilatan, perak, perubahan warna, dan kerapuhan.
Suhu laras terlalu rendah, plastiknya tidak terplastisasi dengan baik, viskositasnya tinggi, kecepatan injeksi lambat di bawah tekanan injeksi dan laju aliran yang sama, produk cetakan mudah tidak mencukupi, tanda las jelas, dimensinya adalah tidak stabil dan terdapat blok dingin pada produk.
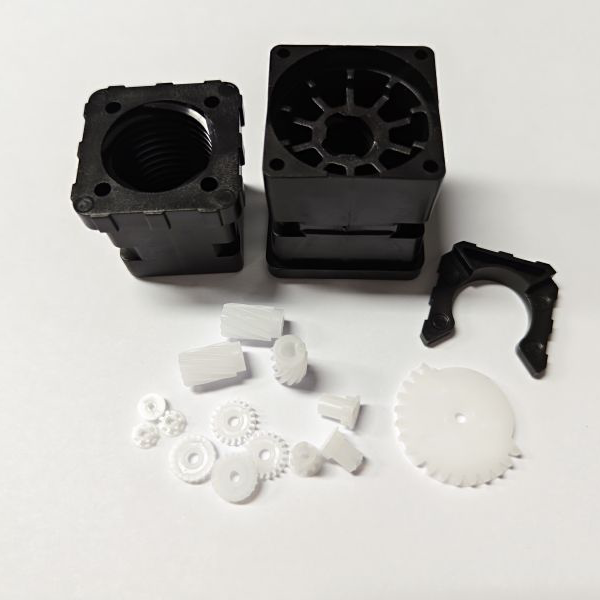
Suhu nosel:Jika suhu nosel diatur tinggi, nosel akan mudah mengeluarkan air liur sehingga menyebabkan filamen dingin pada produk.Temperatur nosel yang rendah menyebabkan penyumbatan pada sistem penuangan cetakan.Tekanan injeksi harus ditingkatkan untuk menginjeksi plastik, tetapi akan ada bahan dingin dalam produk cetakan dengan segera.
Suhu cetakan:Jika suhu cetakan tinggi, tekanan injeksi dan laju aliran dapat diatur lebih rendah.Namun, pada tekanan dan laju aliran yang sama, produk akan mudah berkedip, melengkung dan berubah bentuk, serta akan sulit mengeluarkan produk dari cetakan.Temperatur cetakan rendah, dan pada tekanan injeksi serta laju aliran yang sama, produk tidak terbentuk cukup, dengan gelembung dan bekas las, dll.
Suhu pengeringan plastik:Berbagai plastik memiliki suhu pengeringan yang berbeda-beda.Plastik ABS umumnya mengatur suhu pengeringan 80 hingga 90°C, jika tidak maka akan sulit untuk mengeringkan dan menguapkan kelembapan dan sisa pelarut, dan produk akan mudah memiliki kabel dan gelembung perak, dan kekuatan produk juga akan berkurang.
Bagian Kedua: Tekanan proses pencetakan
Tekanan balik pra-pencetakan:tekanan balik yang tinggi dan kepadatan penyimpanan yang tinggi berarti lebih banyak material yang dapat disimpan dalam volume penyimpanan yang sama.Tekanan balik yang rendah berarti kepadatan penyimpanan yang rendah dan bahan penyimpanan yang lebih sedikit.Setelah mengatur posisi penyimpanan, dan kemudian melakukan penyesuaian besar pada tekanan balik, Anda harus memperhatikan pengaturan ulang posisi penyimpanan, jika tidak maka akan mudah menyebabkan flash atau produk tidak mencukupi.
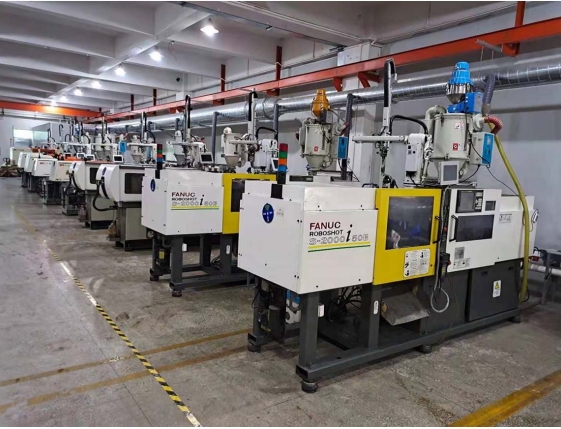
Tekanan injeksi:Berbagai jenis plastik memiliki viskositas leleh yang berbeda.Viskositas plastik amorf sangat berubah seiring dengan perubahan suhu plastisisasi.Tekanan injeksi diatur sesuai dengan viskositas pengelasan plastik dan rasio proses plastik.Jika tekanan injeksi disetel terlalu rendah, injeksi produk tidak akan mencukupi, sehingga mengakibatkan penyok, bekas las, dan dimensi tidak stabil.Jika tekanan injeksi terlalu tinggi, produk akan berkedip, berubah warna, dan kesulitan mengeluarkan cetakan.
Tekanan penjepit:Itu tergantung pada area rongga cetakan yang diproyeksikan dan tekanan injeksi.Jika tekanan penjepitan tidak mencukupi, produk akan mudah berkedip dan bertambah berat.Jika gaya penjepitan terlalu besar maka cetakan akan sulit dibuka.Umumnya, pengaturan tekanan penjepit tidak boleh melebihi 120par/cm2.
Tekanan penahan:Ketika injeksi selesai, sekrup terus diberi tekanan yang disebut tekanan penahan.Saat ini, produk di dalam rongga cetakan belum membeku.Mempertahankan tekanan dapat terus mengisi rongga cetakan untuk memastikan produk terisi penuh.Jika tekanan penahan dan pengaturan tekanan terlalu tinggi, hal ini akan menimbulkan resistensi yang besar pada cetakan penyangga dan inti tarik.Produk akan mudah memutih dan melengkung.Selain itu, gerbang pelari cetakan akan mudah diperluas dan dikencangkan dengan plastik tambahan, dan gerbang di pelari akan rusak.Jika tekanannya terlalu rendah, produk akan penyok dan dimensinya tidak stabil.
Prinsip pengaturan tekanan ejektor dan neutron adalah mengatur tekanan berdasarkan ukuran keseluruhan luas rongga cetakan, luas proyeksi inti inti yang dimasukkan, dan kompleksitas geometri produk cetakan.ukuran.Umumnya hal ini memerlukan pengaturan tekanan cetakan penyangga dan silinder neutron agar mampu mendorong produk.
Bagian ketiga: Kecepatan mesin cetak injeksi
Kecepatan sekrup: Selain mengatur laju aliran pra-plastik, hal ini terutama dipengaruhi oleh tekanan balik pra-plastik.Jika laju aliran pra-pencetakan disesuaikan ke nilai yang besar dan tekanan balik pra-pencetakan tinggi, saat sekrup berputar, plastik akan memiliki gaya geser yang besar di dalam laras, dan struktur molekul plastik akan mudah terpotong. .Produk akan memiliki bintik-bintik hitam dan garis-garis hitam, yang akan mempengaruhi kualitas penampilan dan kekuatan produk., dan suhu pemanasan barel sulit dikendalikan.Jika laju aliran pra-plastik diatur terlalu rendah, waktu penyimpanan pra-plastik akan diperpanjang, yang akan mempengaruhi siklus pencetakan.
Kecepatan injeksi:Kecepatan injeksi harus diatur secara wajar, jika tidak maka akan mempengaruhi kualitas produk.Jika kecepatan injeksi terlalu cepat, produk akan mengalami gelembung, terbakar, berubah warna, dll. Jika kecepatan injeksi terlalu lambat, produk tidak akan terbentuk cukup dan terdapat bekas las.
Mendukung laju aliran cetakan dan neutron:tidak boleh disetel terlalu tinggi, jika tidak, gerakan ejeksi dan tarikan inti akan terlalu cepat, mengakibatkan ejeksi dan tarikan inti tidak stabil, dan produk akan mudah berubah menjadi putih.
Bagian Keempat: Pengaturan waktu
Waktu pengeringan:Ini adalah waktu pengeringan bahan baku plastik.Berbagai jenis plastik memiliki suhu dan waktu pengeringan yang optimal.Suhu pengeringan plastik ABS 80~90℃ dan waktu pengeringan 2 jam.Plastik ABS umumnya menyerap 0,2 hingga 0,4% air dalam waktu 24 jam, dan kadar air yang dapat dicetak injeksi adalah 0,1 hingga 0,2%.
Waktu penahanan injeksi dan tekanan:Metode pengendalian mesin injeksi komputer dilengkapi dengan injeksi multi-tahap untuk mengatur tekanan, kecepatan dan jumlah plastik injeksi secara bertahap.Kecepatan plastik yang disuntikkan ke dalam rongga cetakan mencapai kecepatan konstan, dan penampilan serta kualitas bahan internal produk cetakan ditingkatkan.
Oleh karena itu, proses injeksi biasanya menggunakan kendali posisi, bukan kendali waktu.Tekanan penahan dikendalikan oleh waktu.Jika waktu penahanannya lama, kepadatan produknya tinggi, bobotnya berat, tegangan internalnya besar, proses pencetakannya sulit, mudah diputihkan, dan siklus pencetakannya diperpanjang.Jika waktu penahanan terlalu singkat, produk akan rentan penyok dan dimensi tidak stabil.
Waktu pendinginan:Hal ini untuk memastikan produk stabil bentuknya.Diperlukan waktu pendinginan dan pembentukan yang cukup setelah plastik yang disuntikkan ke dalam rongga cetakan dicetak ke dalam produk.Jika tidak, produk akan mudah melengkung dan berubah bentuk saat cetakan dibuka, dan ejeksinya mudah berubah bentuk dan menjadi putih.Waktu pendinginan terlalu lama sehingga memperpanjang siklus pencetakan dan tidak ekonomis.
Bagian Kelima: Pengendalian Posisi
Posisi perpindahan cetakan adalah keseluruhan jarak pergerakan dari pembukaan cetakan sampai penutupan dan penguncian cetakan, yang disebut dengan posisi perpindahan cetakan.Posisi terbaik untuk memindahkan cetakan adalah agar produk dapat dikeluarkan dengan lancar.Jika jarak pembukaan cetakan terlalu jauh, siklus pencetakan akan menjadi lama.
Selama posisi penyangga cetakan terkontrol, posisi ejeksi dari cetakan dapat dengan mudah dilepas dan produk dapat dikeluarkan.
Lokasi penyimpanan:Pertama, jumlah plastik yang disuntikkan ke dalam produk cetakan harus dipastikan, dan kedua, jumlah bahan yang disimpan dalam tong harus dikontrol.Jika posisi penyimpanan dikontrol oleh lebih dari satu bidikan, produk akan mudah berkedip, jika tidak, produk tidak akan cukup terbentuk.
Jika bahan yang ada di dalam tong terlalu banyak, maka plastik akan bertahan lama di dalam tong, dan produk akan mudah pudar serta mempengaruhi kekuatan produk yang dicetak.Sebaliknya, hal ini mempengaruhi kualitas plastisisasi plastik, dan tidak ada bahan yang dimasukkan ke dalam cetakan selama tekanan dipertahankan, sehingga cetakan produk tidak mencukupi dan penyok.
Kesimpulan
Kualitas produk cetakan injeksi meliputi desain produk, bahan plastik, desain cetakan dan kualitas pemrosesan, pemilihan mesin cetak injeksi dan penyesuaian proses, dll. Penyesuaian proses injeksi tidak hanya dapat dimulai dari titik tertentu, tetapi harus dimulai dari prinsip proses injeksi. .Pertimbangan permasalahan secara komprehensif dan komprehensif, penyesuaian dapat dilakukan satu per satu dari berbagai aspek atau beberapa permasalahan dapat disesuaikan sekaligus.Namun cara dan prinsip penyesuaiannya bergantung pada kualitas dan kondisi proses produk yang dihasilkan pada saat itu.
Waktu posting: 15 November-2023